CNC PROCESSES
CNC Turning Services
Xtmade uses advanced CNC turning centers to machine custom parts for our customers. With multi-axis capabilities, live tooling, and quick-change fixtures, they can produce parts and assemblies to tight tolerances. Contact us for a quote.
CNC Service
Custom CNC Turning Services to Tight Tolerances
Our production floor is climate controlled and away from all sources of vibration. These measures are designed to meet the stringent requirements of aerospace, medical, semiconductor and other advanced technology industries. Turning capabilities include contour, form, taper and line turning as well as single point threading and broaching. Live tooling helps to efficiently machine complex patterns and shapes. Parts can be machined from a variety of alloys such as steel, stainless steel, aluminum, brass and bronze, including difficult to machine specialty alloys such as Invar and Inconel. Our CNC lathes are capable of turning parts up to 13.75 inches in diameter and up to 24 inches in length. Other services include 3, 4 or 5 axis CNC milling, drilling, wire EDM, surface finishing and CMM equipment inspection. We are proud of our years of experience and the team that produces high quality, precision products.
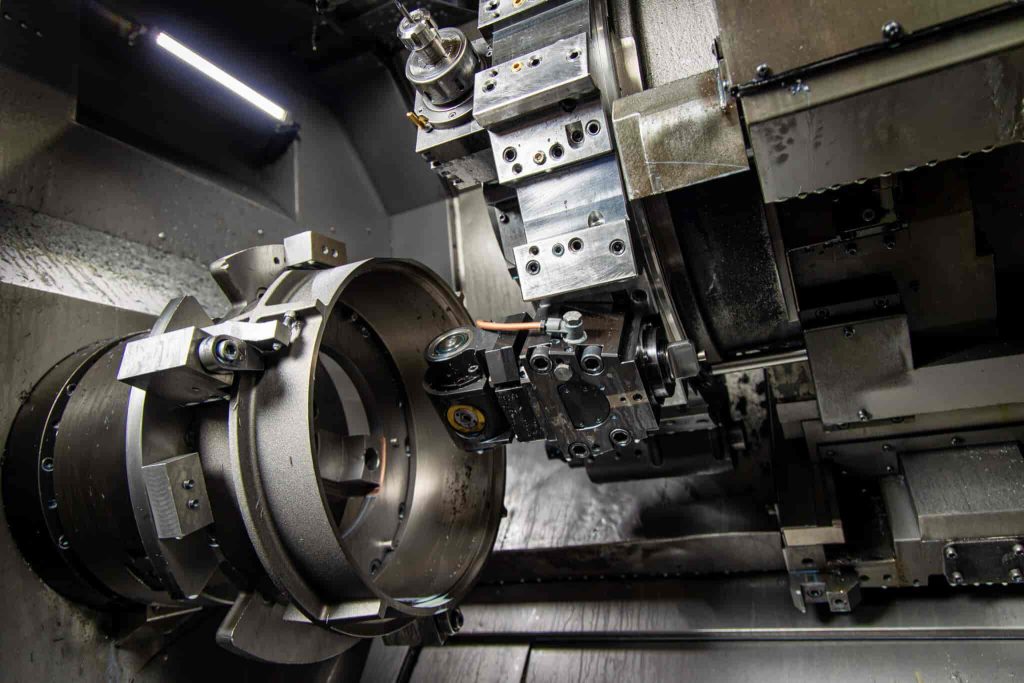
Our Turning Centers
Our turning department features state-of-the-art equipment, experienced personnel, and software to produce your parts quickly and consistently. We specialize in small to medium-sized parts in a variety of materials or complexities with tolerances as low as 0.0001″ (0.0025mm). Chuck capacities range from 6″ to 14″, with 3″ bar capacity, power tools, and a Y-axis. The chuck machines can handle bars up to 2.625″ in diameter, and the Swiss lathes can handle bars up to 1.25″ in diameter. Our chuck machines and Swiss lathes are multi-channel with sub-spindles to allow for the use of multiple tools simultaneously. They also feature bar feeders, power mills with Y-axis, and front or rear part ejection for automated machining.
CNC Turning Tolerances
Our company excels in precision part manufacturing for medical, aerospace, and industrial designs. Using our CNC lathes, we can achieve tolerances of +0.005″, ensuring extremely high accuracy. Metals meet ISO 2768-m and plastics meet ISO 2768-c.
- Maximum Part Size: Typically up to 500mm in diameter and 1500mm in length, but larger sizes can be accommodated with specific equipment.
- Minimum Part Size: Up to 1mm in diameter, depending on material and machining setup.
- General Tolerances: Standard tolerance is ±0.01mm; tighter tolerances as low as ±0.005mm can be achieved depending on part material and complexity.
- Distance Dimensions: +/- 0.005″ for dimensional (length, width, height, diameter) and positional (location, concentricity, symmetry) features.
- Orientation and Form Dimensions: 0-12″ +/- 0.005″, 1/2 degree for angles. For 24″ and others please check Xtmade’s manufacturing standards.
Differences between CNC Turning and Milling
There are some differences between CNC turning and CNC milling. During turning, the workpiece rotates while the cutting tool reduces material. CNC milling takes a different approach, moving the tool along a stationary workpiece. CNC turning is suitable for projects that require cylindrical parts, while CNC milling is suitable for flat machining projects that do not require cylindrical features. CNC milling can be used as a secondary finishing operation to add definition. Complex parts that require prismatic and cylindrical features can use a combination of milling and turning.
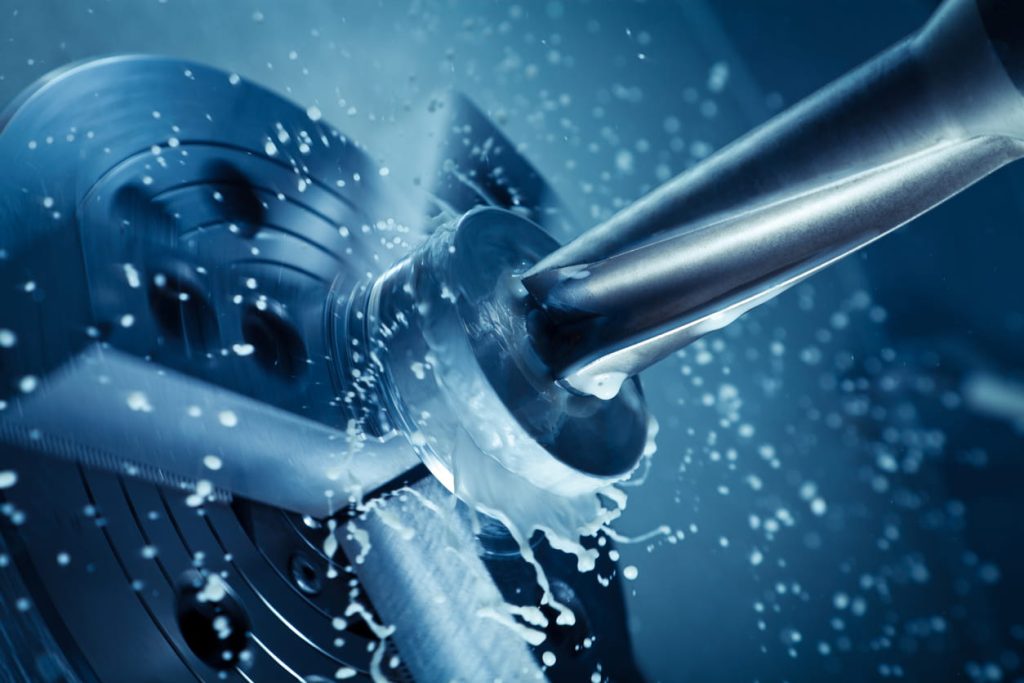

Materials for CNC Turning
We stock a range of metal materials and plastics for a variety of part applications and industries.
- Aluminum
- Brass
- Low Carbon Steel
- Steel Alloy
- Stainless Steel
- Titanium
- plastic
Surface Finishing Options for CNC Turned Parts
With our expertise in CNC turning and surface finishing, we can help you achieve the balance between precision and aesthetics in your machined parts.
- Anodizing
- Bead Blasting
- Powder Coating
- Electroplating
- Polishing
- Brushing
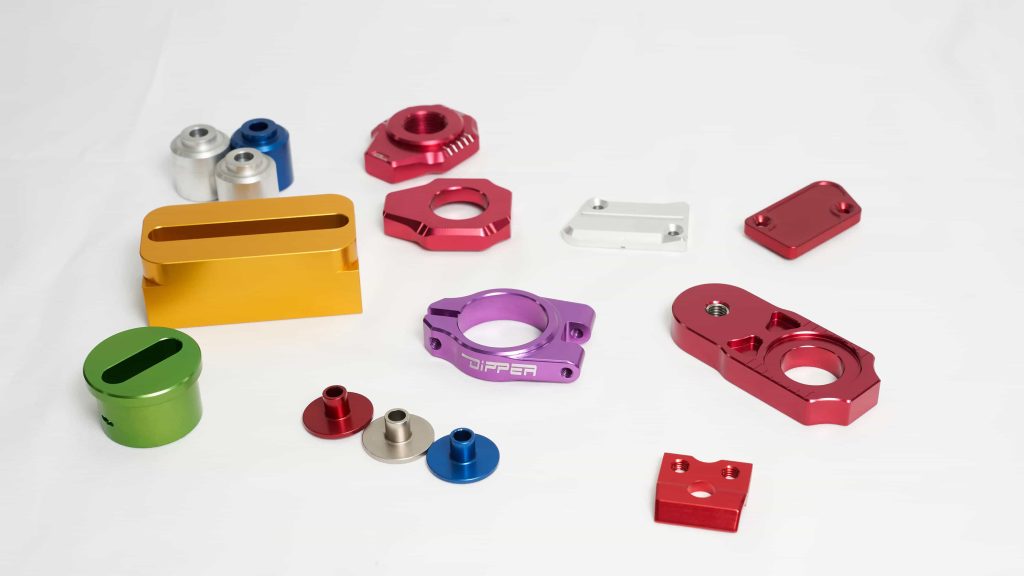
Basic Types Of CNC Turning Processes
CNC turning has a wide range of machining operations that can machine various types of rotating surfaces, such as external turning, internal turning, taper turning, parting off, facing, boring, reaming, drilling, knurling, threading, grooving, etc.
- OD and ID turning: used to machine precision cylindrical features. Used to machine precision cylindrical features. The turned part can continue to be machined to a depth with visible tool marks (Tools used: Universal turning tools)
- Parting off and grooving: used to cut or cut “groove” profiles inside or outside the part (Tools used: Parting off and grooving inserts)
- Facing: Flattening the surface of the workpiece (Tools used: Facing tools)
- Boring and reaming: Enlarging or finishing existing holes to obtain high-precision diameters (Tools used: Boring and reaming tools)
- Drilling: Removing material to drill a hole from the inside of the workpiece (Tools used: Drills)
- Threading: The production of threads by turning can be performed on the internal or external areas of the workpiece. (Tools used: Threading tools)
What is CNC turning?
CNC turning is a type of machining within CNC machining and is one of the common techniques within subtractive machining technology. The basic operation is to hold a material such as plastic or metal in place with a chuck. The workpiece rotates on the lathe, and the computer-controlled turret and attached tools cut the material into the specified shape according to the programmed instructions. The more tools the turret can accommodate, the more complex the options available for the part. CNC lathes and turning centers can utilize a variety of processes to create different end results.
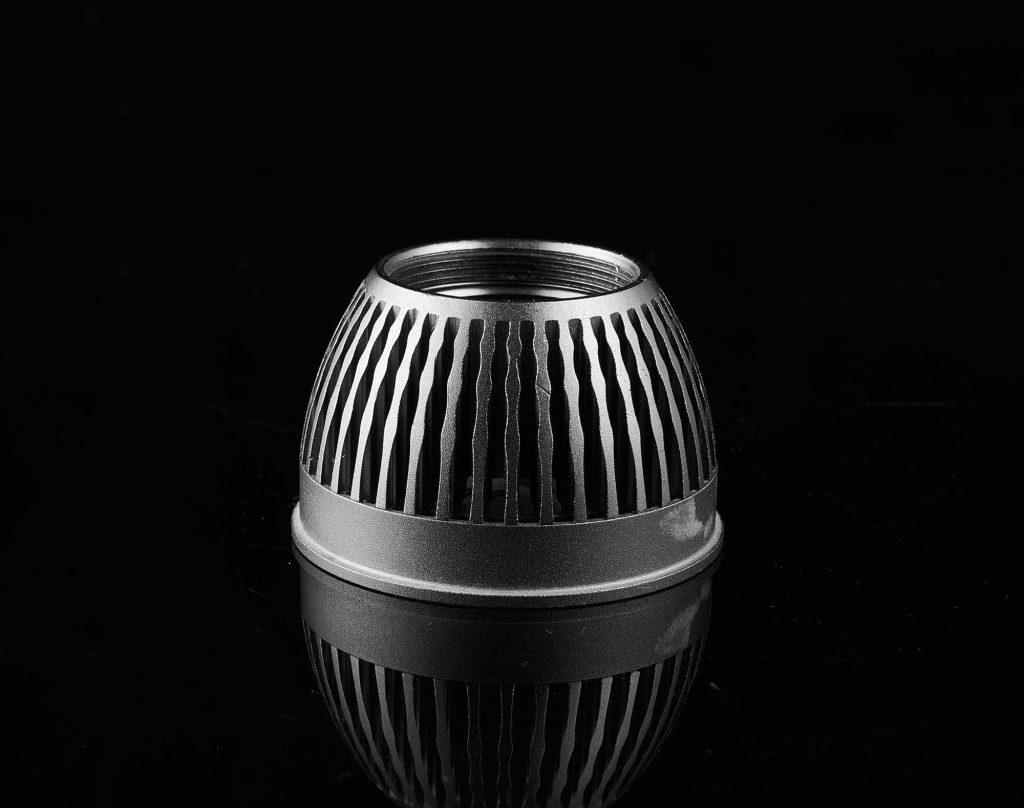
Quality Management
At xtmade, we understand that every project is unique, which is why we offer a range of materials to meet our customers’ needs. Whether you need a part made from aluminum, stainless steel, or another metal, we have the expertise and resources to deliver the results you need. Our commitment to quality is reflected in every aspect of our CNC turning services, from the choice of materials to the rigorous quality control processes we implement. We pride ourselves on providing parts that meet the highest quality standards, and we are committed to exceeding our customers’ expectations.
Industries We Serve
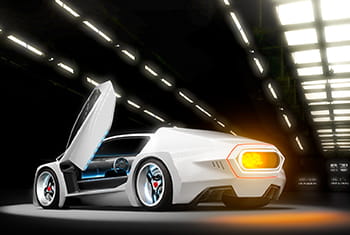
Automotive
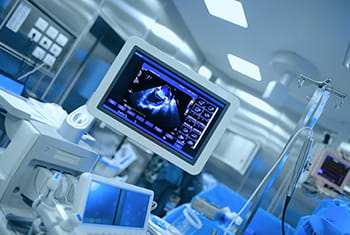
Medical
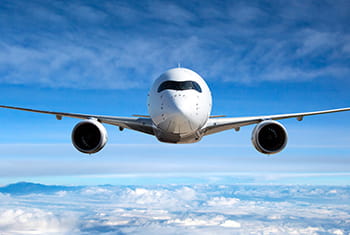
Aerospace
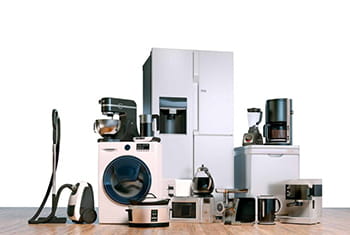
Consumer products
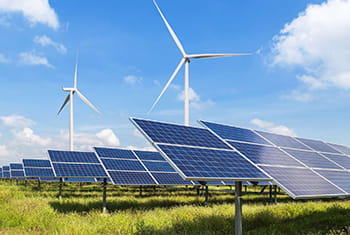
New Energy
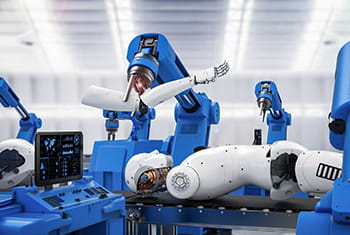
Industrial machinery
Are you ready to start your next CNC turning project?
Once you send us your 3D CAD file for a free quote, one of our customer service engineers will check the manufacturability of your design to ensure the part meets your expectations and budget requirements.
Latest News
Xtmade team summarizes technical issues related to CNC machining
The CNC machining industry needs to solve problems…