Plastic parts manufacturing
Injection Molding Services
With our unique combination of superior skills and expertise, we can make better plastic parts tailored to your needs and preferences. Our full range of custom injection molding services enables us to work with you every step of the way. Accelerate iterative testing and scale production. Upload your designs now for DFM feedback and pricing.
Meeting your fast tooling and low-volume production needs
We have the experience and equipment to deliver unmatched speed, flexibility, and support. We leverage our exceptional molding expertise to provide comprehensive technical guidance and tooling options for your project. We don’t just send a price estimate for a new project; we send an informed quote after understanding your needs. We work closely with you from the beginning to ensure the job specifications match your project goals.
Plus, we offer fast turnaround on injection molding services without sacrificing quality or precision. We continually improve our production processes, implementing new methods to reduce inefficiencies and shorten lead times for our customers. Whether you’re looking for short-run production, rapid tooling, or prototyping services, we can help you find the best solution and deliver it quickly and efficiently.
We are experts in understanding the complexity of our customers' needs for a wide range of plastics
Xtmade offers the widest range of plastic injection molding services to meet your needs. We are industry experts who continually seek to improve our reaction injection molding process by contributing significant design knowledge and capabilities.
Each of our members is dedicated to making your RIM design a success at every stage of the production process. From part and CAD design to mold design, manufacturing, part production, secondary operations, painting and screen printing, assembly, packaging, shipping, and more, we are here to serve your project.
Explore Our lnjection Molding Service
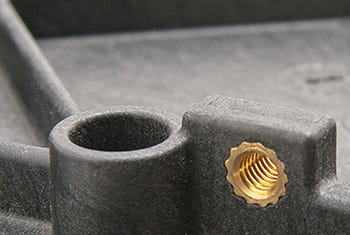
Insert Molding
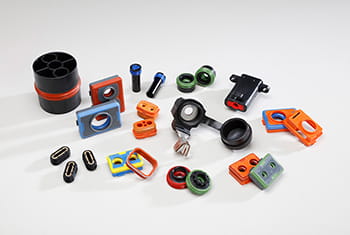
Overmolding
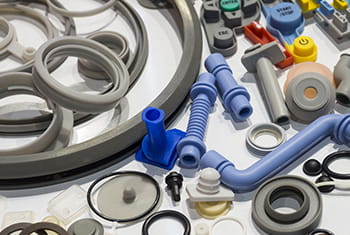
LSR Molding
Injection Molding Materials
We make quality plastic injection molded parts, Xtmade offers common metals and a variety of popular plastic materials for injection molds. If you are looking for alternative material options, contact our team of engineers today.
Hard Plastics
- ABS (Acrylonitrile ButadieneStyrene)
- ASA (Acrylonitrile StyreneAcrylate)
- CA (Cellulose Acetate)
- COP0 (Copolyester)
- PCTI (Polycyclohexylenedimethylene Terephthalate)
- PPA (Polyphthalamide)
- HDPE (High-Density Polyethylene)
- PEEK
- Polypropylene (PP)
- Polycarbonate (PC)
- PMMA (Polymethyl Methacrylate, Acrylic)
- Nylon 12(PA12)
- Nylon 6/66(PA6/66)
- Derlin (PoM)
- Teflon (PTFE)
- PBT
- PLA (Polylactic Acid)
- High-Density Polyethylene(HDPE)
- PVC
- PPS (Polyphenylene Sulfide,Ryton)
- Vespel (Pl)
- Torlon 4203 (PA)
- UPE/UHMW
- PVDF
- ULTEM (PEI)
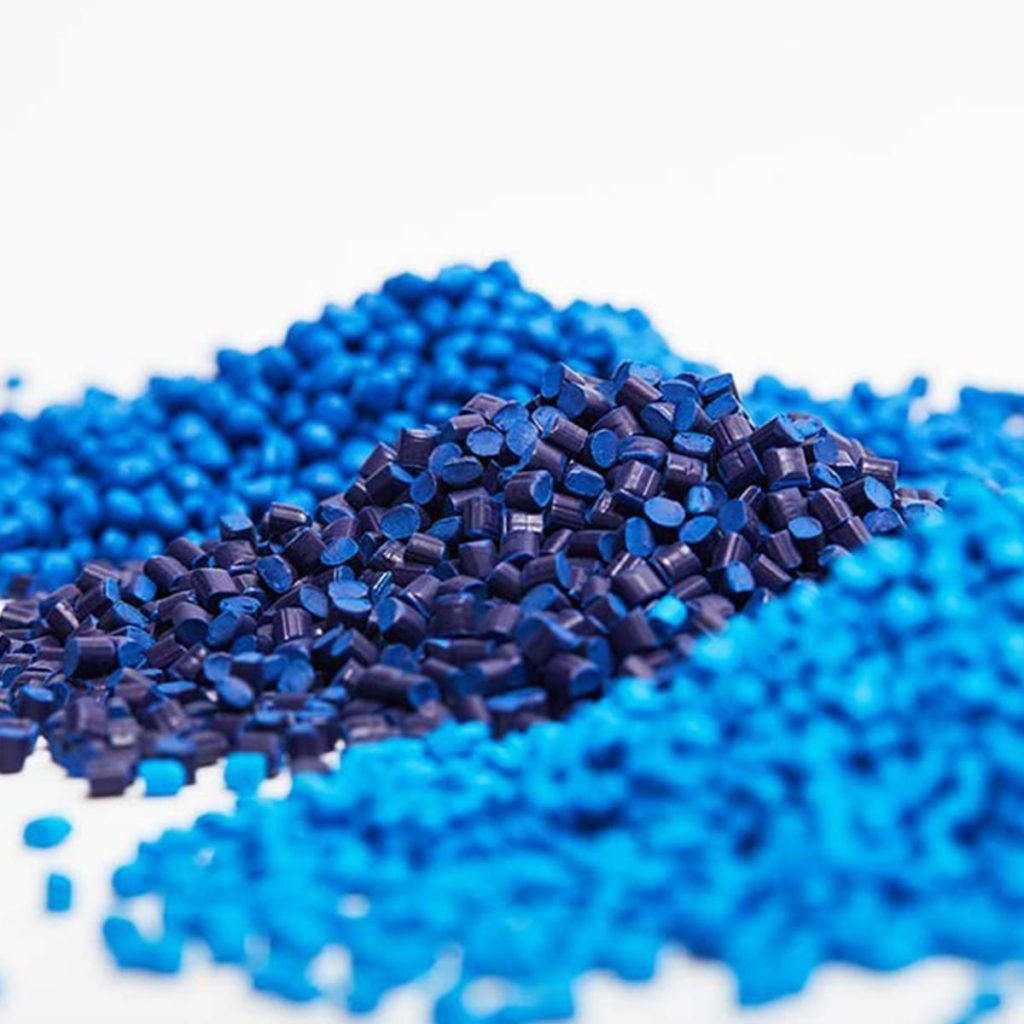
Mixed plastic
- PC-ABS (Polycarbonate-Acrylonitrile ButadieneStyrene)
- PC-PBT (Polycarbonate-PolybutyleneTerephthalate)
- PC-PET (Polycarbonate-PolyethyleneTerephthalate)
- PS-PPE (Polystyrene-Polyphenyl Ethers)
- PE-PS (Polyethylene-Polystyrene)
- PE-PP ( Polyethylene-Polypropylene)
- PBT-PET(Polybutylene Terephthalate-Polyethylene Terephthalate)
Rubber-Like Varieties
- TPE (Thermoplastic Elastomer, Santoprene)
- TPU (Thermoplastic Polvarethane (Shore A)
- LSR (Liquid Silicone Rubber)
- PVC (Polyvinyl Chloride (Shore A))
- POE (Polyolefin Elastomer)
- MPR (Melt Processable Rubber)
- EPDM (Ethylene Propylene Diene MonomerRubber, Viton)
Flexible Plastics
- Polyethylene (PE)
- Polystyrene (Ps)
- PET
- EVA Foam
- EPS Foam
- PU Foam
Ready to Get a Custom Injection Molding Quote?
Overview of our injection mold making services
Our core competence in mold making lies in the following three stages:
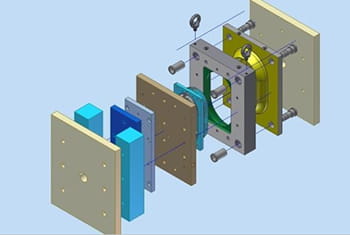
Mold Design
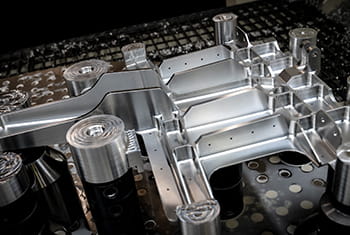
Mold Machining
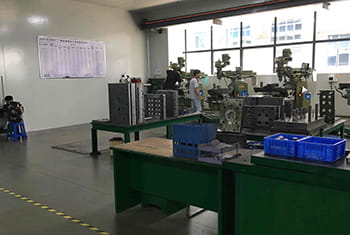
Mold assembly
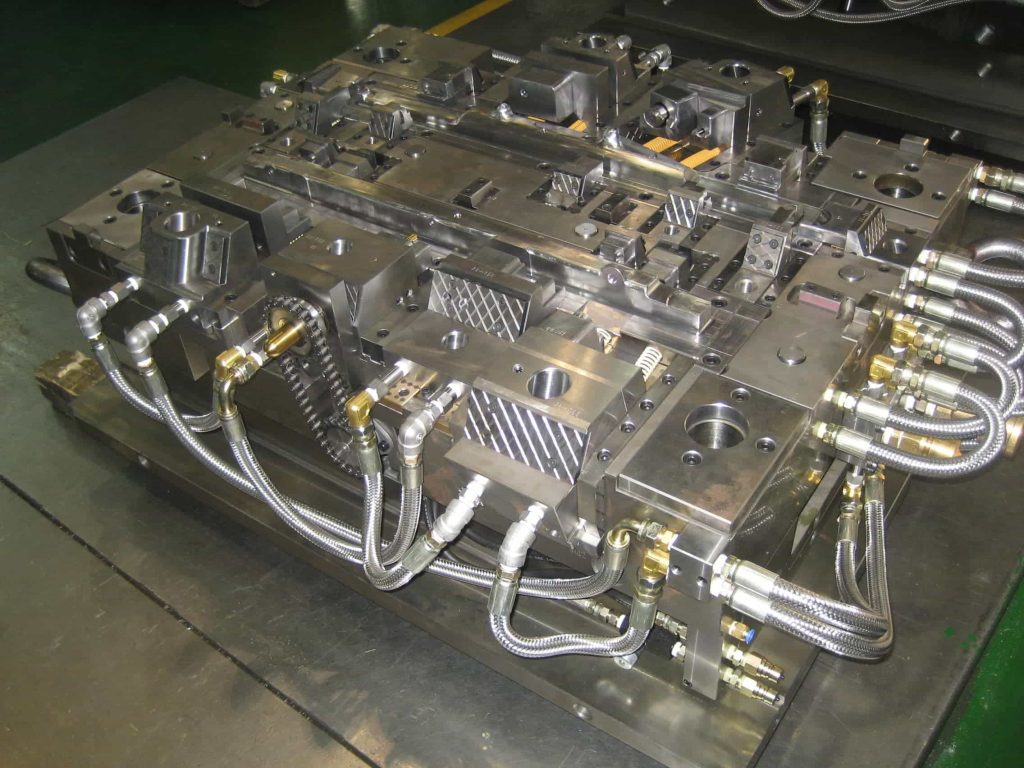
Precision Mold Manufacturing Technology
In our state-of-the-art facility, we utilize cutting-edge technology to deliver custom injection molds of the highest precision. Our factory-customized equipment enables complex designs, ensuring impeccable accuracy and repeatability during mold manufacturing. By utilizing advanced technology, we guarantee molds that meet or exceed industry standards, resulting in superior product quality and performance.
Tailor-made Product Design Solutions
We understand that every product design is unique, with specific requirements and challenges. Our factory-made custom injection mold solutions provide the flexibility to meet these individual needs. We have a dedicated team of engineers who work closely with our customers to fully understand their design goals and complexities. This personalized approach ensures that the mold design is optimized to produce a product that meets or exceeds expectations while reducing production time and costs.
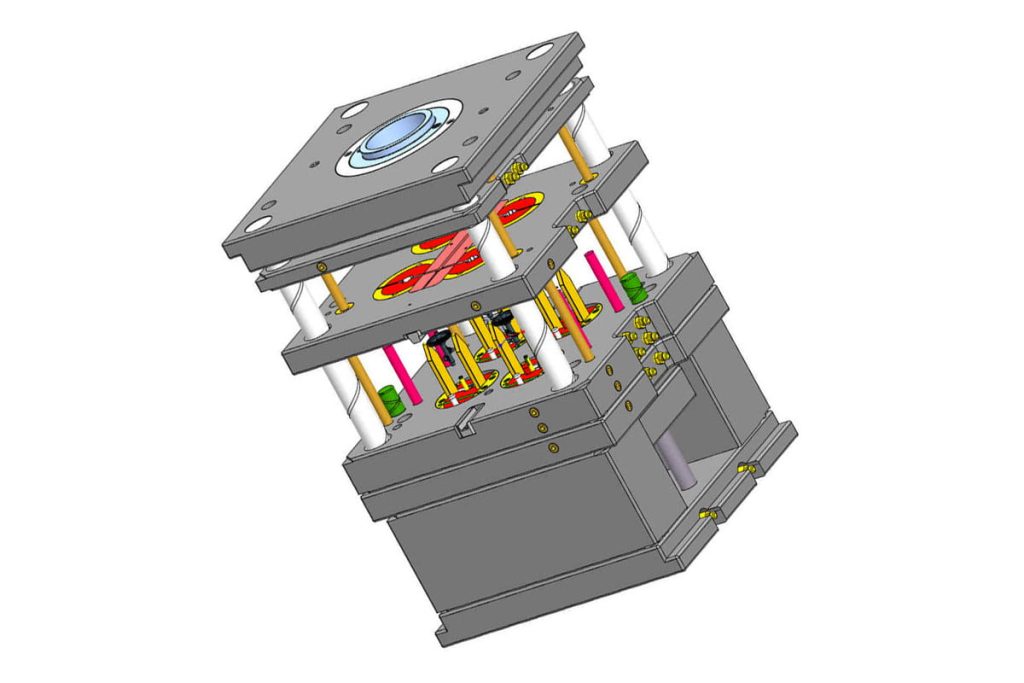
Injection Mold Types
We can manufacture injection molds from aluminum (ideal for rapid low-volume prototyping) or tool steel. Molds conform to the SPl mold classification, which specifies the durability of the mold and the number of cycles it can handle.
Standard injection mold tooling is defined by classes from Class 105 (prototype) to Class 101 (highvolume production). These mold classes help manage expectations for both customers and suppliers onthe overall tool requirements and scope.
Over 1,000,000 cycles. They are engineered for extremely high production. This is the highest-priced moldand is made with only the highest-quality materials. Class 101 molds are also known as Class l tools.
Example: Multiple-cavity steel tooling with full automation and overnigh work centers for dedicated part manufacturing.
Medium to high production tooling, suitable for abrasive materials or parts requiring close tolerance. Thisis a high-quality, reasonably high-priced mold. Class 102 Molds are also known as Class ll tools.
Example: Steel tooling with an SPl A-2 finish, automated slides, scheduled production cycles.
Under 500,000 cycles. Medium production mold. This is a very popular mold for low to medium production needs. Most common price range. Also known as a Class lll tool.
Examples: aluminum or steel tooling, automated lifts or slides, multiple repeat run batches between 1,000-5,000 units.
Under 1 00,000 cycles. Low production mold. Use only for limited production, preferably with non-abrasivematerials. Low to moderate price range. Class 104 molds are also known as Class iV tools.
Example: Aluminum or MUD tooling, SPl B-3 finish, hand-loaded cores, and limited re-runs.
Under 500 cycles. Prototype only. This mold will be constructed in the least expensive manner possible toproduce a minimal quantity of prototype parts. Class 105 molds are also known as Class V tools.
Example: a one-and-done market test of 100 molded units.
What is Injection Molding?
The injection molding process begins with plastic resin pellets. The resin is heated to a molten state and then shot into the mold. The plastic pellets are loaded into a hopper that feeds the injection molding machine. The pellets are fed by gravity from the hopper into a heated chamber (called a barrel) where they are melted, compressed, and injected into the mold’s runner system by a reciprocating screw. Runners are channels in the mold that deliver molten plastic to the mold cavity.
The pellets are slowly moved forward by a spiral plunger, and the molten plastic is forced through a nozzle connected to the mold’s sprue bushing, which controls the flow of material through the gate and runner system into the mold cavity.
The metal mold is kept at a lower temperature so the plastic solidifies almost immediately after the mold is filled. The part cools and hardens into the shape of the mold cavity. The two halves of the mold, the A and B sides, or the cavity and core, open, and the ejector pins push the part out of the mold, where it falls into a box. The mold is then closed and the process begins again.
Advantages of Injection Molding
- Using plastic injection molds, you can produce large quantities of uniform, complex parts and geometries.
- Injection molded plastic parts are compatible with a wide range of colors and materials, including resins, silicones, thermoplastics, and thermosets.
- An injection mold is one of the strongest guarantees that a part will match the original. This not only ensures brand quality and part reliability, but also reduces plastic material waste.
- Due to the simplicity and consistency of the process, injection molding is the perfect solution for scaling up large-scale or batch production. Standardized injection molds enable manufacturers to produce to the specific requirements of their products and replicate them quickly and accurately.
- After paying for the setup costs, the price per unit of a product manufactured through injection molding drops dramatically and remains at an extremely low level. The more parts produced, the lower the unit cost, which makes plastic injection molding particularly suitable for large-scale production.
Focus on small and medium-volume orders
Low volume plastic injection molding is primarily driven by customers with continuous product development cycles or low product demand. Xtmade works with product developers, OEMs and tier suppliers to deliver plastic injection molded parts that meet tight specifications, timelines and budgets.
Our ideal customers for low volume molding highly value supplier relationships, understand that price is an element of total cost, and utilize Xtmade as their preferred partner in plastic product development to troubleshoot, propose solutions and share best practices in tool design and optimized processing for repeatability shot after shot.
We encourage potential customers to bring their next plastic development project to Xtmade to experience firsthand what our team has to offer!
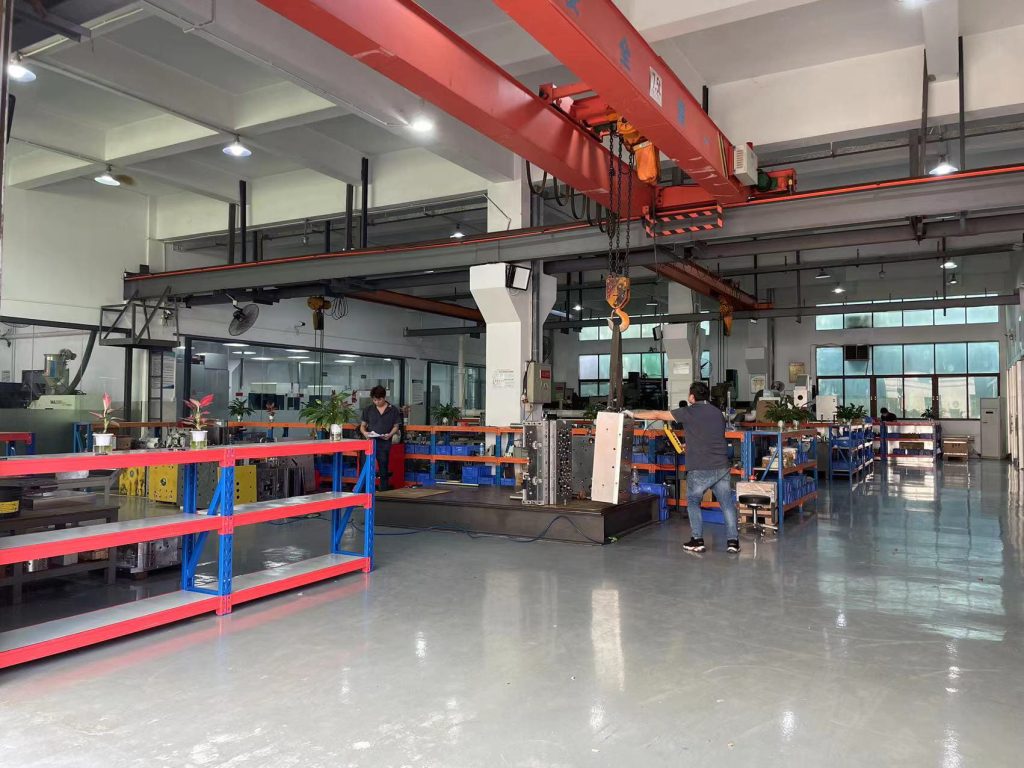
Industries We Serve
We serve companies in many industries, including automotive interior and exterior accessories, medical device components, safety components, and more.
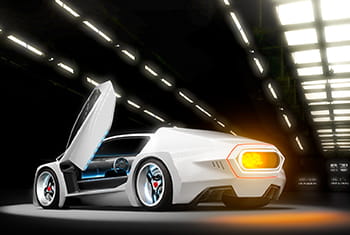
Automotive
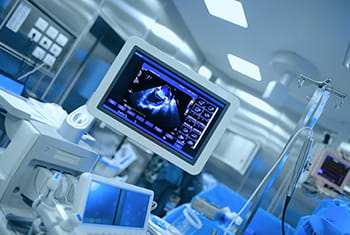
Medical
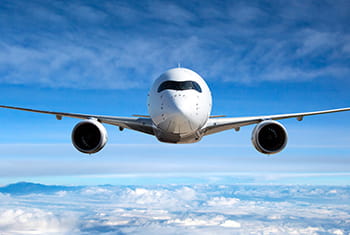
Aerospace
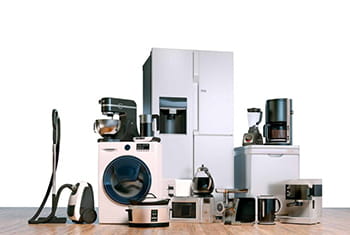
Consumer products
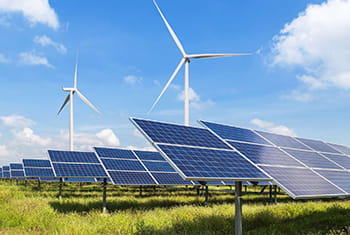
New Energy
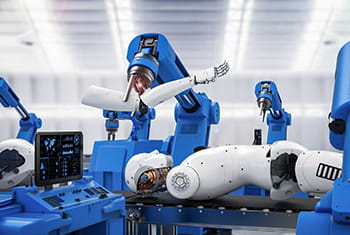
Industrial machinery
Want to start your injection mold project now?
We provide high-standard injection molding services, support fast delivery of small batch manufacturing, and respond quickly within 24 hours.